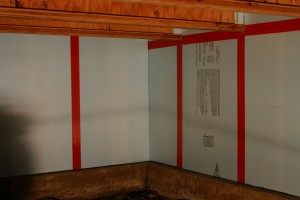
The foam board in this basement is in the process of being air sealed with tape at the joints and corners.
Concrete basements in many older homes are inadequately insulated by today’s standards (or not insulated at all). For new construction, both state and local building codes require a minimum R-value of 15 for below-grade walls (walls buried in soil).
This makes good sense as the soils in our region are relatively cold; even below the frost line, soil temperature may only reach a high of 36°F.
This means that in a poorly insulated basement, significant heat losses can occur year round. Basement walls that are well sealed and insulated, on the other hand, can save money and make yourhome more comfortable.
In older homes, it is often more practical to insulate the basement from the inside. If there are any problems with water penetration, make sure you fix them first or any work you do on the inside will be compromised.
If gutters and good site drainage don’t solve a water problem, then unfortunately excavating the exterior and applying a coat of waterproofing and resolving drainage issues may be necessary.
Rigid foam board or high-density spray-applied foam insulation make good choices for basement walls. Both products are resistant to air flow and can tolerate occasional exposure to small amounts of moisture. Depending on the type of foam, it will take between 3 and 4 inches to produce the minimum R-value of 15. Remember that the concrete behind the insulation is cold and will attract condensation if it is exposed to inside air.
If you use rigid foam board, then the joints should be tight, taped and also staggered if you are using several layers.
Be aware that building codes are strict regarding exposed foam in living spaces, and almost all foam insulations will have to be protected with some type of fire-proofing.
Once the foam is in place, then wood framing or furring can be used to run wiring and plumbing, and to provide an attachment for Sheetrock (which is a fire protection). Often, using a plastic vapor retarder is not advised if you will be insulating the basement walls with foam board. If properly sealed, the foam provides a good air barrier, and a layer of plastic sheeting will only reduce the wall’s ability to dry out, should moisture ever make its way in.
Basement walls that are well sealed and insulated can result in big energy savings and increased comfort. But because this area of your home will become much tighter, you may need to consider some form of mechanical ventilation to insure good air quality and humidity control.